The evolution of batteries in the oil & gas industry
Published: 09 August, 2023
Batteries play a pivotal role in both the oil and gas and subsea industries, acting as the main or back-up power source for a wide range of equipment, from pipeline inspection gauges and downhole drilling tools to underwater vehicles and smart buoys. Here, Robert Brown, Marketing Executive at Ultralife, highlights common and unique challenges that each piece of equipment faces and outlines best practice power considerations for each one.
Electronic devices used in the subsea or oil and gas industries are exposed to harsh conditions, such as the high temperature and inaccessibility of a pipeline or the perishing cold and remoteness of the ocean floor. These conditions are not only faced by the devices themselves but every component inside them, down to the battery. Addressing these issues is an essential requirement for both device and battery designers, to ensure functionality and safety.
Key battery design choices
Reliability and long lifespan are both vital specifications of many downhole and subsea batteries. This is because they are used in devices that operate in isolated environments where maintenance is impractical or impossible.
Mass-produced consumer batteries can deteriorate quickly under these conditions, causing them to fail prematurely and resulting in costly downtime. To combat this, specially designed commercial batteries have been produced by manufacturers who specialize in serving sectors where power failure is not an option (such as Ultralife who manufacture for the military and medical sectors too).
These manufacturers produce batteries that are certified to high standards of safety and quality but that also serve the specific needs of each individual piece of equipment, which we will explore below.
Measurement while drilling
Measurement while drilling (MWD), logging while drilling (LWD) and directional drilling equipment call for batteries designed to withstand exceptionally aggressive drilling environments.
The battery and drilling tool it powers must be squeezed into a tight pipeline where they will be exposed to high temperatures (up to 200°C) and pressure. Only non-rechargeable Lithium Thionyl Chloride (LiSOCl2) cells offer the size to power ratio (energy density) and heat resistance required. These cells should be connected into packs to increase voltage and/or capacity. Robust internal welds and solder joints must be used and rated to meet the temperature, vibration and shock needs of the application.
Additionally, a smart gauge should be used to provide reliable data on how much life is left in the battery and to present a trustworthy record of downhole conditions, which can be used to verify the tool’s own findings.
A design engineer should also carefully consider epoxy, encapsulant, heat shrink, and battery casing, which can be done in conjunction with the battery manufacturer.
Pipeline inspection batteries
Regular pipeline inspection is essential for ensuring the safety and integrity of oil and gas pipelines. The internal inspection of pipelines is normally carried out by intelligent inspection devices called pigs (so-called because of the porcine squeal they emit when squeezed into the pipe) or scrapers. The electronics in the pigs, including the batteries and solid-state drives used to record the data must be well-sealed and protected against damage to either themselves or the pipeline.
Pipeline conditions are close to those encountered whilst drilling (e.g., tight-fitting), although the temperature is not as high. Non-rechargeable Lithium Thionyl Chloride cells are still recommended for this application and should be built into durable packs that meet power, environmental and safety requirements.
Subsea batteries
Subsea batteries play a critical role in powering offshore equipment, including remotely operated vehicles (ROVs), autonomous underwater vehicles (AUVs), and other underwater systems. Available space in an underwater vehicle is not as non-negotiable as in a pipeline but higher voltages are needed; so rechargeable batteries are used.
As the depths and distances these vehicles are tasked to explore becomes greater, endurance and run time become key issues that should be addressed first when specifying a battery.
Ultralife has designed its rechargeable subsea batteries to offer four times longer endurance and run time when compared to sealed lead-acid (SLA) alternatives, thanks to their high energy density and advanced chemistry.
As with MWD and LWD applications, it is beneficial to use condition-based monitoring and other built-in smart gauge functions to monitor the health of the battery in real-time.
Smart buoy batteries
Unlike drilling and subsea applications (where the remote locations or tightly sealed devices make charging impractical), buoys are floating above the water, making the batteries that power them much easier to access and charge.
Each year, smart buoys, marine signaling buoys, mooring buoys and data buoys get packed full of increasingly more sensors and monitoring devices that allow them to report on a larger amount of weather and sea conditions, providing essential data for the oil and gas industry. Furthermore, some buoys can also be used to generate electric power from wave movement that can power offshore oil and gas equipment.
With an increase of sensors and equipment inside the buoy comes a reduced space available for the power solution. Buoys traditionally used sealed lead acid (SLA) batteries, but these are increasingly being supplemented by smaller, more power dense, rechargeable lithium iron phosphate (LiFePO4) alternatives. Up to 20% of a buoy’s weight was previously taken up by traditional SLA solutions but today only up to 7% is, thanks to LiFePO4.
Both SLA and LiFePO4 batteries can be charged by the sun, using solar panels connected to the battery, which is ideal for an application like smart buoys that have constant exposure to the sky. Furthermore, lithium iron phosphate batteries are easy to maintain, as – unlike sealed lead acid – they can be mounted in any direction, so there is no longer the necessity to dismount the entire buoy. Plus, LiFePO4 batteries last up to seven times longer than SLA and require no physical maintenance during that time.
Overall, the key features a design engineer should look for in all oil and gas and subsea applications include long run times and high energy density. However, there are some considerations (down to whether a non-rechargeable or rechargeable battery should be used) that depend on the specific piece of equipment.
In applications that include drilling, engineers should consider the extreme conditions that the battery must operate in, such as high vibration and temperatures. In pipelines, it is important to consider how reliable the battery is, because it will be sealed inside the pig and not easily accessible.
In applications like subsea, considerations include how long the offshore equipment will be submerged for and, therefore, the required battery runtime. In contrast, batteries for smart buoys can be changed regularly, but space is more of a concern.
Contacting a subsea or oil and gas battery expert can ensure that the correct selections are made, ensuring that both the device and its power solution are fit-for-purpose. This should be complimented by local engineering support, to provide confidence that difficult installations and maintenance can be handled with ease. Ultralife has nine locations across three continents, including manufacturing facilities in the oil state of Texas, USA and near the North Sea (UK).
https://www.ultralifecorporation.com/
https://twitter.com/UltralifeCorp
https://www.linkedin.com/company/ultralife-corporation
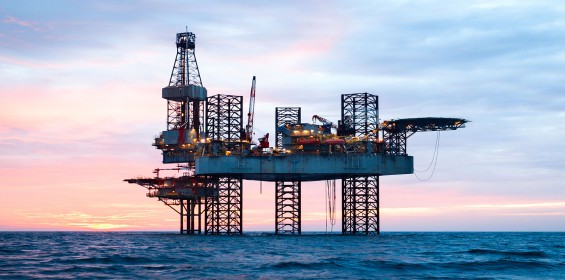