New investment expands welding capabilities
Published: 13 April, 2022
UK-based oil and gas subsea equipment specialist Express Engineering has announced a six-figure investment in new precision welding equipment and capabilities as it expands its sector operations to support customers.
The move comes as the company completes its relocation to its new 48,000 sq. ft. assembly and test centre in Gateshead. It also sees the relocation of the welding department to a newly refurbished facility with the addition of a new carbon steel specific welding area with an additional buttering/cladding station for larger parts up to five tonnes, automatic butt-welding and manual fabrication.
AMI (Arc Machines Inc.) narrow gap equipment butt-welding has also been added to improve the capability to deposit lower weld volumes on downhole tooling for the offshore sector, increasing productivity and reducing distortion on heavy wall thickness butt-welds.
New 20 tonne capacity Fronius endless torch rotation (ETR) cladding equipment has also boosted capabilities. This will allow complex geometry welding of racetracks and cross or intersecting bores to be completed in one single operation, providing additional precision engineering cost and time savings.
Alongside investment in extra equipment, two new welders have joined to provide increased both cladding and butt-welding capacity while Express Engineering’s trainee welding engineer has qualified as a CSWIP 3.1 welding inspector as part of continued professional development.
Additional investment equips Express Engineering with a comprehensive range of welding capabilities, enhancing its ability to undertake straight forward cladding projects to complex cladding requiring ETR, regular pipe butt-welding and specialist narrow gap welding. Fronius cladding stations, TipTig automated butt-welding systems, an AMI orbital pipe welding system and several manual GTAW (Gas Tungsten Arc Welding), MIG (Metal Inert Gas) and MAG (Metal Active Gas) systems are all available.
Gary Thirlwell, managing director, said investment in additional precision welding capabilities will provide advantages over other conventional systems as well as applications.
He said: “We now offer a full range of specialist welding services, ranging from simple corrosion resistant overlay (cladding) all the way to precision pipe welding and fabrication in exotic alloys. We are developing products for all areas of oil and gas exploration and production, from the inter-surface arena to below-the-mud line operations.
“Our extended capabilities will see us not only able to improve the support current oil and gas customers enjoy, but also expand our precision welding services into a wider range of industrial applications such as the nuclear and defence sectors.”
The investment also comes as the company continues to expand the scope of turnkey solutions provided to the global energy sector, particularly as it moves further into the development of new below-the-mudline products. A range of precision-engineered ‘Measurement While Drilling’ (MWD) and ‘Logging While Drilling’ (LWD) tools have also recently been produced as part of new product development projects for international energy technology companies.
Express Engineering is a leading manufacturing, assembly and testing specialist for the subsea energy sector. Working with customers like TechnipFMC, Baker Hughes and Aker Solutions, the company is a significant exporter of products, operating within various geographical areas, including the North Sea, Gulf of Mexico, east coast of Brazil, east and west coasts of Africa and Australasia.
More at https://express-engineering.co.uk/ or contact sales@express-engineering.co.uk
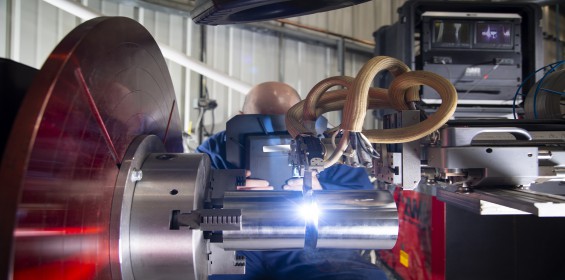
Express Engineering has invested in new precision welding equipment and capabilities as it expands its sector operations to support customers