Dare to defer? Decide by data
Published: 21 April, 2021
When it’s not possible to deliver on every aspect of an integrity management plan – and for many operators, that issue was especially acute in 2020 – how do you address the deferral dilemma? The answer lies in making the best possible use of another valuable operational asset: data.
Christopher Blake, head of new business for IMRANDD
The myriad of complexities posed by COVID-19 made it harder than ever for operators to stick to their planned inspection programmes last year. But, while the pandemic restrictions certainly exacerbated the challenge, it was hardly a new phenomenon.
The average safety critical backlog rose by 44% between Q4 2018 and Q4 2019, according to OGUK’s Health, Safety and Environment Report 2020. Most of the increase, says the report, stemmed from deferrals. It throws into sharp relief the quandary faced by asset and integrity managers as they try to articulate where their inspection priorities – and deferral options – lie.
Resource and schedule constraints are of course the main root causes behind deferrals, but issues can come into play if regulatory approval is the only or main thrust of the tactical response.
In tightly regulated locations like the United Kingdom Continental Shelf (UKCS), regulatory bodies maintain a watchful eye over integrity management plans and most will require clear and robust technical justifications for the rescheduling of safety critical inspections. However, the narrow regulatory view for deferrals does not appreciate all the opportunities in which deferral plans can be better optimised. This being so, regulatory approval should be considered as a benefit of a well-considered deferral plan, but there will always be a higher bar to achieve.
There are also, of course, in-house imperatives driven by safety, optimisation and efficiency, which often gives way to a difficult balancing act. In pursuit of efficiency, operators will sometimes defer a non-critical inspection without considering the implications, for example this could lead to greater maintenance costs down the line. In other cases, inspections are performed that could reasonably have been pushed back – taking away time from inspections that would have caught failures in the making. Some of these decisions were undoubtedly taken because the integrity team was unable to leverage a dataset or lacked confidence in the data available.
Trust in data?
This highlights a wider conversation around the perceived lack of trust in some areas of asset integrity around the use of data – and it also poses the question of whether we can and should move on from our conventional inspection practices. More strategic asset management, using the available resources to hand – not least, easily extracted, robust data – could take us in a new, even safer and more cost-effective direction. It’s a strategic issue we’re very focused on at IMRANDD.
Deferral justifications can take many forms; they may involve time-consuming reviews of past data, alongside intermediate or non-intrusive inspections to satisfy assumptions that deferral is acceptable. Or operators might take the condition of some items in a suite of equipment – a set of ballast tanks, for example – as representative of all of them and push inspections of some tanks back a year, confident in the assertion that degradation levels are lower than had been anticipated and, in any event, a failure wouldn’t compromise the overall integrity of the wider asset.
But, rather than extrapolating the available information, what if the operator had actual data on the actual piece of equipment and harnessed that knowledge to make fully informed deferral decisions? It’s generally accepted that, as an industry, we’re good at collecting asset data – but we come up short in harnessing it and then deploying it to material advantage.
Data-based deferrals
There are three key outputs when you build a data model based on the comprehensive digital knowledge of a piece of equipment. Firstly, you gain a better understanding of the likelihood of failure under certain conditions and over a set period of time. With knowledge you can monitor for changes to those conditions and are empowered to seek the resources to inspect within the appropriate timescales.
Secondly, it provides the ability to understand where you may be over-inspecting. From here, you can then target inspection resources with much greater efficiency while also underpinning your deferral justifications to regulators.
Finally, a robust model can also expose potential gaps in the availability of quality asset data, and these gaps can then be closed through targeted inspection, reviewing wider industry knowledge or by supplementing your model with additional data.
Our AIDA data analytics tool, which equips operators to better understand both legacy data and the ever-growing levels of new data generated by technological advances, provides these outputs and more. The software solution mitigates risks because decisions are based on solid, reliable data; on hard evidence. By forming a data model of the degradation of a particular asset, we’re moving away from the principles of inspecting to either find a defect or confirm its absence. Instead, we’re curating the data model so it’s more accurate and more representative of the overall condition of the asset: a tool, a resource, that’s constantly updated and driving decisions by looking at the performance of an asset in a more holistic way. Using this approach, the value from inspection shifts from only being gained when a defect is found, to all outcomes that can improve the data model.
Smoothing the road ahead
If you’re simply inspecting in the here and now for individual areas of corrosion or other prospective failures, you’re not necessarily understanding the overall condition of the piece of equipment and – critically – what issues may lie around the corner. It’s perhaps comparable to driving a car along a street: instead of constantly looking down for potholes or other imminent accident hazards, it’s safer to be looking up at the road ahead. You’re seeing the bigger picture and anticipating, in the longer terms, where the pitfalls might lie.
Our optimisation tool REFLEX also leans into the data to support the execution of plans as efficiently as possible, and is based on assessing available resource (staff, bed space) against schedules, time and cost. It helps operators manage both the peaks of activity – where they’re having to make decisions based on priorities – and the troughs, where there are opportunities to make best use of resources and get more work done. The two solutions are in many respects closely intertwined in terms of aligning safe deferral decisions and reshaped inspection programmes. Indeed, REFLEX can be strategically key in first optimising asset activities and therefore informing any deferral process.
Safety critical backlogs, and the need for a robust deferral plan will no doubt always be something that asset and integrity managers will need to contend with. However, by leveraging existing data using tools such a IMRANDD’s AIDA and REFLEX, operators can become better equipped to pursue a strategy that makes best use of resources, at the right times, to deliver on their long-term safety, operational and commercial objectives.
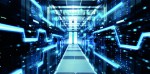