Costly leakage rate eliminated
Published: 17 February, 2021
For a gasket to do its job effectively, it is essential that the seal it creates remains intact over a long period of time. The gasket must also be resistant to fluids and/or gases and withstand the operating temperatures and pressures to which it is subjected. For many applications, these qualities are best achieved with adhesive gasketing products in preference to pre-cut, compression gaskets.
The main reasons why compression gaskets leak or fail are poor surface contact and their tendency to relax under load and decrease in thickness, with subsequent loss of bolt tension in the flange joint. High stresses on the gasket can also cause it to crack, tear, rupture or to be squeezed out between the flanges.
By comparison, a liquid gasketing product fills all voids to create a perfect seal between components, with maximum face-to-face contact, eliminating flange face corrosion. It has high resistance to solvents, resists high pressure when cured and there is no need for re-torquing.
A wide range of adhesive gasketing products are available for different flange types, gap sizes and material but careful consideration of the performance criteria is essential as one manufacturer of cast iron gearboxes and geared motors can attest. Although it had opted for liquid gasketing on the adapter assembly flange the adhesive was causing issues in both production and the long-term reliability of the end-product.
It was estimated that a poor seal was causing a 5% leakage rate. This was proving costly due to testing and production delays caused by the adhesive’s slow cure rate and also leakage-related warranty claims on purchased units. The adhesive also made it difficult to dismantle the geared motor for maintenance and repair.
Having re-assessed its technical requirements and trialled alternative brands, the manufacturer found a LOCTITE gasket sealant met all performance criteria. The product chosen was LOCTITE 518 which effectively fills the gaps between the flange surfaces and cures quickly so close-fitting parts can be instantly pressure tested to 276 kPa (40 psi). Leaks have now been eliminated and disassembly is easier for customers.
Formulated for rigid iron, steel and aluminium flanges, LOCTITE 518 is applied as a continuous bead or by screen printing to one flange surface. A roller pen version is also available.
For more information go to: www.henkel-adhesives.co.uk
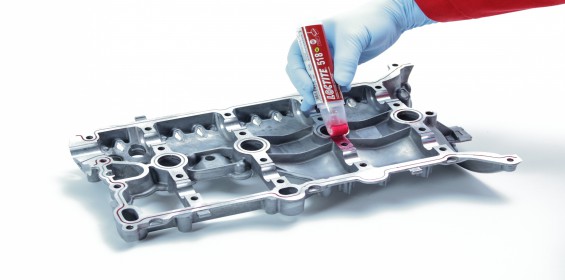