Ceramic bearings for subsea applications
Published: 16 August, 2023
Subsea applications are characterised by constantly harsh conditions and extreme environments. In marine environments, various applications involve propeller shafts and components for underwater robots and telecommunication systems. However, in the presence of water, salt, and harsh elements, selecting just any bearing won't suffice — it's crucial to choose the right one for optimal performance and durability. In the article below Chris Johnson, Managing Director, at specialist bearing supplier SMB Bearings, examines the potential of ceramic bearings in marine environments.
The World Corrosion Organization has reported that the global annual cost of corrosion amounts to a staggering US $2.2 trillion, equivalent to more than 3% of the world's gross domestic product (GDP). When a bearing in a subsea industrial application begins to experience corrosion, it sets off a chain of detrimental effects.
Firstly, the corrosion accelerates wear on the bearing’s raceways, rolling elements and cages. This heightened wear, coupled with the compromised surface integrity, increases the bearing's susceptibility to the intrusion of abrasive particles and contaminants. These contaminants can further exacerbate wear and damage in critical components such as seals, gears, and other bearings, leading ultimately to further failures, increased maintenance and replacement costs.
Swift intervention and the use of corrosion-resistant bearings are vital to mitigate these risks and ensure the integrity and longevity of subsea equipment.
The lifespan of a bearing can be significantly affected when it is fully submerged, depending on the material composition. Take 440 grade stainless steel bearings as an example. While they exhibit high resistance to fresh water and weak chemicals, they are prone to rapid corrosion when exposed to salt water or fully immersed in water.
440 grade stainless steel bearings struggle to withstand the corrosive nature of these environments, even with external protection such as passivation, leading to reduced performance and premature failure.
Passivation involves a metal finishing process that utilises nitric acid or citric acid to eliminate free iron from the surface. This chemical treatment results in a protective oxide layer, reducing the likelihood of chemical reactions with air and preventing corrosion. However, in a marine environment, without protection from the elements, the passivated metal will eventually corrode. So, which material is ideal for subsea applications?
Ceramic bearings excel in corrosive environments, although they may come at a higher initial cost. Ceramic bearings, such as Si3N4 bearings, don’t react with saltwater and many harsh chemicals, which can add consistent performance even when they are permanently submerged. This characteristic provides subsea operators with a reliable bearing solution that enhances operational efficiency, and reduces downtime associated with maintenance and replacements.
Reduced friction and wear
Ceramic bearings offer significantly lower friction coefficients compared to their steel counterparts, resulting in reduced energy consumption, improved overall system efficiency and increased lifespan.
The materials Zirconia (ZrO2) and silicon nitride (Si3N4), for ceramic bearings, both have excellent corrosion resistance. As these materials have a low friction coefficient, they can even be used without lubrication in lower speed applications. The exceptional hardness of ceramic materials also contributes to lower wear rates, extending the service life of the bearing and reducing downtime for maintenance and replacements.
Resistance to debris and contamination
Subsea environments often expose bearings to the risk of debris, sand and other contaminants. Traditional steel bearings will suffer from accelerated wear and failure under such conditions.
Because of their much greater hardness, ceramic bearings exhibit improved resistance to particle intrusion, although care should be taken to prevent contaminants from entering any bearing to ensure reliable operation. This feature lessens the risk of failure and enhances the durability of subsea equipment.
Non-magnetic properties
In applications such as subsea telecommunication systems, the choice of bearing is critical to ensure reliable and efficient signal transmission across undersea fibre optic cables. Ceramic bearings offer significant advantages in this context, making them an ideal choice.
One of the key benefits of ceramic bearings is their non-magnetic properties, which play a crucial role in preventing electromagnetic interference with signal transmission. As subsea telecommunication systems rely on precise data transfer over vast distances, any magnetic interference could lead to signal disruptions and data loss.
By utilising non-magnetic ceramic bearings, these systems can maintain the integrity of their signal transmission, ensuring uninterrupted communication between continents and enhancing the overall reliability and performance of subsea telecommunication networks.
SMB Bearing’s full ceramic bearings, made from zirconia or silicon nitride with PEEK cages and seals, offer superior corrosion resistance in marine applications. Since ceramic bearings are not affected by seawater, they can be used in marine environments where they are permanently submerged and can cope with higher loads.
Ceramic bearings are mainly used in environments that are too hostile for steel bearings, where heavy shock loads are unlikely – due to the brittle nature of ceramics. SMB Bearings ZrO2 bearings possess several advantageous properties. They are non-magnetic and non-conductive, making them suitable for various applications.
Additionally, they exhibit high corrosion resistance against a wide range of chemicals. Their water resistance further enhances their suitability for marine applications, particularly in fully submerged scenarios or situations where the load or speed exceeds the capabilities of 316 marine grade bearings.
Because corrosion comes at a high cost and can cause wear and tear on bearings, choosing the most suitable bearing material at an early stage can help subsea operators prevent downtime, unplanned rework and costly replacement parts. Investing in ceramic bearings, which are completely corrosion resistant and have a long lifespan, will help avoid disturbing the application and maintain a steady workflow.
https://twitter.com/SMBtechgeeks
https://www.linkedin.com/company/smb-bearings/
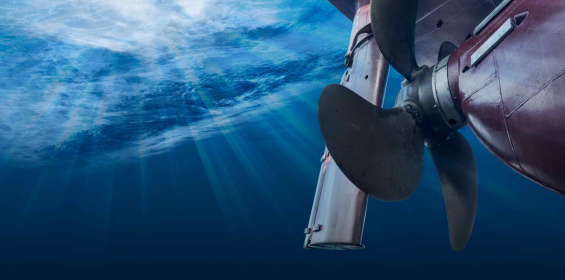