Ex-proof hydraulics for offshore mooring systems
Published: 19 July, 2023
OEE takes a look at Ex-proof hydraulics for offshore mooring systems.
Improved corrosion resistance, heavy equipment handling and potentially explosive area - all the strict requirements typical of the energy and offshore sector are together combined in mooring systems for oil & gas vessels, for which ex-proof electro hydraulics represents the most widespread solution, meeting all the mentioned requirements, as well as ensuring highperformance controls and simple maintenance.
Moorings: a key equipment of oil & gas offshore units
Mooring systems are a key equipment of offshore units deployed for petroleum and gas production, as they allow any floating platform to be safely held in position, avoiding risks or potential damages coming from rough sea waves.
Spread-mooring, tower systems and turret-type solutions: different executions are available on the market, but they all share the same key features, from the necessity to handle heavy equipment and strong forces – e.g. catenaries or winches – to the strict requirements of the offshore oil & gas sector, such as the need for improved corrosion-resistance, the application of specific international norms and the mandatory use of explosion-proof certified products due to the presence of petroleum and gas.
Ex-proof hydraulic systems are therefore the most widespread solution for the actuation of mooring systems, as they meet offshore requirements with long-term operative life, allowing also to perform high-performance motion controls
Electrohydraulic systems for moorings
A typical ex-proof electrohydraulic system for a mooring application comprises a central HPU for the Power Generation and various hydraulic manifolds directly mounted on the deck equipment, so that the control valves are as close as possible to the winches and the actuators.
Ex-proof solenoid valves are present in every actuation: on/off valves are used for simpler or auxiliary movements, while proportional valves or cartridges are generally applied whenever higher performances are required. A typical example is the Chain Jack System, where high-flow ex-proof proportional valves control the reciprocating movement of a big-bore cylinder used to haul-in and tension the mooring chain.
The hazardous area is typically classified according to the IEC 60079 directive as zone 1 for overdeck installation, requiring explosion-proof certification for hydraulic components and electrical equipment.
As for corrosion resistance, manifolds, valves and actuators are usually protected with dedicated marine painting cycles with thicknesses up to 300 ?m, while piping and fittings are generally stainless steel made. Although, whenever the installation involves a particularly weathered location or very low temperatures, it is not uncommon to use ex-proof stainless steel valves.
Wide range of ex-proof hydraulic components
The classification of potentially explosive areas within oil & gas vessels could vary according to ship section. For example, process systems located underdeck are typically classified as Zone 0 requiring Ex-i intrinsically safe valves, while overdeck mooring systems are usually classified as Zone 1 requiring flameproof Ex-d valves combined with certified Ex-h actuators and pumps to prevent eventual risks caused by hot surfaces or mechanical moving parts.
One company that offers a complete ex-proof range of multicertified electro hydraulics components for applications in potentially explosive environments, from on-off valves to the complete systems is Atos:
Ex-proof proportional valves with on-board digital technology allow smart solutions developed for industrial sector to be extended also to hazardous locations, like the last generations fieldbuses, built-in oscilloscope for advanced diagnostics, high performance axis and pq control.
The range includes specific on-off executions aimed to further increase the safety level in hazardous environments, like exproof solenoid valves certified up to SIL2 / SIL3 according to IEC 61508 or ex-proof directional valves with inductive proximity sensors to monitor the spool position.
Ex-proof power units and hydraulic blocks designed for marine environments classified as hazardous locations are certified by TÜV, DEKRA, UL, CSA, ABS, BV, DNV GL, RINA: high production quality, strict compliance to customer specifications and specific marine painting cycles are only some of the key factors which Atos Systems Division says makes it the preferred hydraulic partner for the offshore sector.
For further information please visit: https://www.atos.com/
https://www.linkedin.com/company/atosgroup/
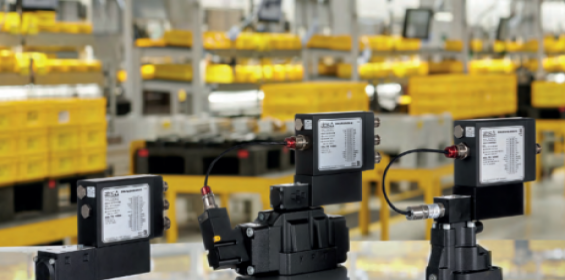