Critical spares and repairs of hydraulic cylinders for large petrochemical company
Published: 27 April, 2022
A large crude oil petrochemical company realised it didn’t have any critical spares for hydraulic cylinders within important valves from the pipeline. The company required new cylinders to replace the old ones, but did not want a long period of downtime, due to the financial loss that this would mean.
However, due to the age of the cylinders (several decades old), there were no reliable drawings available from which to manufacture like-for-like replacements. Apex Hydraulics was consulted, and it was decided that Apex would take the originals and repair them in as brief a time as possible – while also getting measurements to manufacture new cylinders that could then be kept as spares. A brief shutdown period was planned.
Materials pre-order
Apex Hydraulics requested some basic measurements and some photographs, to allow a pre-order of the materials that would be required for the repairs. The engineers knew that some of these materials may be required, and others would be redundant if not needed – however, none would be wasted, as anything not used on the repairs could be kept for the manufacture of the new cylinders. Some basic manufacture was started even before the cylinders arrived.
On the agreed date, the petrochemical plant shut off the three valves and removed the hydraulic cylinders. Two faces had rusted together, so it was very labour intensive to get the pin out. Because of this, although the three cylinders were expected to reach Apex together, they arrived at different times. However, once the first cylinder had been stripped and assessed it allowed parts to be prepared for the other two cylinders, meaning work was not delayed too much.
A short deadline
When the cylinders reached the workshop there was a mammoth effort to get the repairs turned around on time, with Apex staff working up to 12 hours a day to meet the client’s deadline of completing the work within four days.
All cylinders were entirely dismantled to be assessed. Two of the cylinders were leaking and required new cylinder rods. All had the bores polished, the components cleaned and dimensionally checked, and they were all assembled with replacement like-forlike seals. The client wanted to send one of its own engineers to witness the entire process, which Apex Hydraulic was happy to facilitate.
Non-destructive testing
The client wanted an external inspector to carry out Non-Destructive Testing. This involved a specialist procedure in which any minor flaws or defects (not visible to the naked eye) could be detected in the original materials. First, a deep red stain was sprayed onto all components of the entire cylinder, left for a short period and then wiped off. The red dye would get into any microcracks in the steel. Secondly, a white chalk-like material was sprayed on top, which, when activated by a magnet, drew any remaining red dye onto it, making any cracks or imperfections visible. Happily, the original steelwork was still of very good construction, but the NDT allowed for full peace of mind for the client.
During the repairs, drawings were made of the cylinders so that like-forlike replacement parts can be made for the company, so there would be no downtime the next time maintenance is required. Apex is currently manufacturing these spares.
https://twitter.com/apexhydraulics
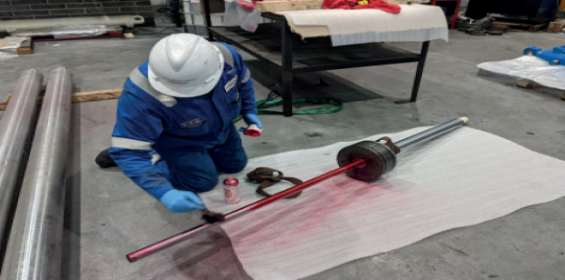