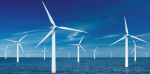
Offshore wind turbines: tough nuts to crack
Published: 23 August, 2021
The risks of climate change now need little introduction. We are already starting to live with the impacts of a changing climate on communities, businesses and supply chains. The most recent Intergovernmental Panel on Climate Change (IPCC) report delivered the unnerving news that we now have less than a 9-year window to act on climate and limit global warming to 1.5 degrees Celsius. It made plain that limiting warming to 2°C will not be enough to prevent the most serious impacts.
To limit global warming to below 2°C and as close as possible to 1.5°C, the world must reduce net greenhouse gas emissions to net zero by mid-century. To achieve that, we must electrify as many economic activities as possible, use hydrogen primarily made from electricity in many others, and totally decarbonise electricity supply. Other technologies such as carbon capture and storage or use (CCS/U) and sustainable bioenergy will also need to be deployed. But clean electricity will be at the core of the zero-carbon economy, fuelling many sectors of the economy, including road transport and building heating. It is estimated that electricity’s share of final energy demand will grow from only 20% today to over 60% by mid-century.
Wind energy – the key to direct electrification
Governments, industry and NGOs across the globe are focused on reducing dependence on conventional sources of energy in order to curb our carbon footprint. The urgent need for dependable, clean, and cheap power is expected to drive the future energy market. Governmental policies and regulatory frameworks to provide a favourable environment for industry to promote renewable power generation is expected to propel both the solar and wind energy market growth globally.
The wind energy market was valued at over USD 125 billion in 2020 and is estimated to grow by 4% CAGR between 2021 to 2027, with annual installation anticipated to exceed 120GW by the end of that period. Although the wind energy industry was no an exception to the impact of the COVID-19 pandemic – causing delays in both project execution and the flow of supply chains – 2020 was the best year to date for the global wind industry showing year on year (YoY) growth of 53%. With more than 93 GW of wind power installed in what was such a challenging year demonstrates the resilience and significance of the wind industry.
The onshore segment has until recently accounted for the largest share of wind turbines – as much as 94.8% in 2019 – mainly down to ease of installation and its low cost over offshore wind power. However, offshore deep-water sites are gradually gaining in importance, with total offshore wind capacity now exceeding 35 GW, representing 4.8% of total global cumulative wind capacity.
Wind energy companies are increasingly shifting towards offshore wind farms as they have proven to be more efficient as compared to onshore installations. This is due to higher wind speeds and greater consistency in direction. For this reason, fewer turbines are required to produce the same capacity of energy than those installed onshore. Wind Europe (formerly the European Wind Energy Association) estimates that an average onshore wind turbine with a capacity of 2.5–3 MW can produce more than 6 million kWh in a year – enough to supply 1,500 average EU households with electricity, yet an average offshore wind turbine of 3.6 MW can power more than 3,312 average EU households.
As technology continues to improve and project executions begin to reach critical mass, the cost of offshore wind turbines is forecasted to drop significantly. That being the case, manufacturing techniques to deliver ultra-high strength, cost efficient turbine monopiles at pace will remain a key focus for the industry.
Performance standards – the key to success
Offshore wind energy turbines are often situated in some of the roughest and most inhospitable seas, and have to be able to withstand enormous loads from huge waves and mighty swells. High quality steel and the most up to date production methods are necessary for wind farms operating under such harsh conditions. In this context, welding becomes particularly important as the huge steel towers and support stilts that the turbines are composed of, are manufactured from several individual steel segments. A faulty weld seam on a single component can have catastrophic consequences. Cracks or dangerous saltwater corrosion could lead to a rupture in one or more the steel components.
Performance standards for wind turbine components, particularly those operating offshore, therefore confront manufacturers with tough challenges. In the case of standard steel constructions, fully automatic systems for the heat treatment of weld seams have been in place for some time, but for segments of wind turbine towers – steel plates which are up to 30 metres long, 4 metres wide and 12 cm thick – such systems are as yet non-existent.
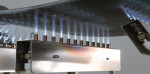
Welding in this application can be a challenging affair. The thick metal components need to be pre-heated, and if not done, the large, cold steel plates will lose heat too quickly which can lead to faulty welds, making a secure connection impossible. Pre-heating will prevent the build-up of cold cracks, which can occur at the same time due to several reasons: hardening in the heat affected zone (HAZ) during welding, the combination of residual and load stresses and load stresses and hydrogen embrittlement.
This is particularly important when treating high strength steels. After the weld, these materials must be post-heated for several hours to diffuse any rogue hydrogen atoms in the weld seam. For manufacturers who have to maintain a fast production speed, it is vital that they quickly reach a pre-heated temperature of greater than 100 degrees Celsius.
The LINDOFLAMM solution, which is based upon Linde’s pioneering acetylene-based burner technology, has proved to be the ideal technology for this application, delivering preheating and post heating treatment solutions for heavy steel manufacturers and fabricators. An important characteristic of acetylene is the high heat intensity in the primary flame. This results in a focused flame, pre-heating only in the weld area, increasing the speed at which weld area is heated, as much as a two thirds’ faster than other fuel gases and significant savings on total process cost.
As opposed to a propane gas flame, for instance, acetylene gas burns with a very precise, pointed, so-called ‘primary flame cone’, which drives the heat directly into the metal. Additionally, the flame temperatures that can be reached with the associated acetylene-compressed air torch – approximately 2,400 degrees Celsius – are significantly higher than those achievable using other fuel gases in combination with air. The new burner is therefore capable of heating up the steel twice as fast as conventional methods.
As an additional assurance to wind turbine and other offshore renewable energy structure manufactures, Linde has committed to the strictest of assessments via the “type testing” of its LINDOFLAMM® burner portfolio. Type testing is a rigorous conformity assessment – approached from mathematical, physical, chemical and logical perspectives - across an extensive number of variables involved in determining a process, product, or service. As such, it goes well beyond simple regulatory compliance to meet the highest levels of modern-day conformance requirements in terms of specifications, technical standards, regulations and contracts. Linde is the only atmospheric gas suppliers to guarantee their technology to such a high standard.
As a result, Linde is leading the field in terms of pre- and post-heating welding applications for offshore wind turbine towers.
Florian Lang, expert thermal processes Linde, author
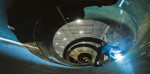