When it comes to safety offshore, we can’t ignore the warning signs
Published: 11 May, 2021
See below for a blog post from David Jamieson (pictured), founder and MD of Salus Technical. Having analysed the HSE’s safety reports and enforcement notices from the past 4 years, David identified a number of common significant safety challenges offshore, and also offers some advice on how to address these. It’s a very pragmatic analysis of the current situation, trends in safety issues and some straightforward recommendations for tackling these.
Picture the scene. You are at a swimming pool. There are two lifeguards on duty. You learn that one of them recently saved the lives of two people, on separate occasions. The second has never had to perform an emergency rescue. But which is the ‘better’ lifeguard?
Personally, I’d put my trust in the latter. Why? Well, in the words of Futurama, “When you do things right, people won't be sure you've done anything at all.” While lifeguards are trained to respond to life-threatening situations, their most important job is undoubtedly incident prevention.
The same applies to safety in the oil and gas industry, where being proactive and taking action before an incident occurs is imperative. And while there are many moments worth celebrating, there is also room for improvement. We must not take our eye off the ball.
In exploring these areas further, I analysed two key sources of information. The Health & Safety Executive’s (HSE’s) Offshore Statistics & Regulatory Activity Reports and its online library of enforcement notices from across the past four years, of which there are approximately 160.
There is some good news. Fatalities and injuries are in decline, with no fatal injuries since 2016, and the number of ‘over-7-day’ injuries reported dropping from 86 in 2018 to 73 in 2019.
An area where we are falling short is hydrocarbon releases. So much so that, in 2018, the director of the HSE’s energy division, Chris Flint, wrote to all North Sea oil and gas operators, outlining his concerns over unplanned gas releases. Despite this intervention, the number rose from 100 in 2018 to 126 in 2019. As well as this, over the last four years, at least 1 in 4 offshore topic inspections across all disciplines has resulted in a score of either poor or very poor, meaning that they are ‘significantly’ below the standard expected by the HSE.
Further, of the 160 aforementioned enforcement notices, 30 were due to hydrocarbon releases that had occurred. That means 30 instances were deemed significant enough to warrant enforcement action being taken by the HSE. When you consider that one hydrocarbon release is one too many, this is a cause for concern.
Failures during isolation and reinstatement of plant constitute one of the main causes of ‘loss-of-containment’ incidents. This emerged as another common theme, with 13 enforcement notices issued by the HSE in the last four years due to inadequate process isolations.
There are a number of factors that may have contributed to this. One being that, over time, we may become desensitised to risk. Our mindset, and the actions we take or don’t take, are crucial in managing risk.
As OGUK’s former supply chain manager, Matt Abraham, said in 2019, “A sense of chronic unease has to be maintained.” That’s because even the weakest signals could lead to a much bigger event – as illustrated by the Mendocino Complex fire in northern California in 2018, caused by something as innocuous as a “spark or hot metal fragment landing in a receptive fuel bed.”
The complexity of process engineering and the cumbersome nature of process isolations is another factor. This is particularly true on older assets where it is sometimes impossible to execute certain tasks while achieving the required process isolation. Often, we need to deviate from the accepted standard, which isn’t exactly a recipe for success.
In a previous role, as an engineering technical authority, I often had to say “No, you can’t do the job as planned because it falls short of the required standard.” Those are tough conversations to have; not because people are trying to be difficult, but because some requirements can be hard to understand or appear overly onerous.
The HSE’s ‘The Safe Isolation of Plant and Equipment’ (HSG253), sets out its expectations for process isolations clearly. A document I often refer to, it is what most isolation standards are based on. Of course, writing and issuing a standard is not the end destination; you’ve got to roll it out properly so that those who need to know, do. I’m also a big advocate for standards and procedures that are written in such a way that, if a deviation is required, the required action is clearly and simply laid out.
Poor alarm management also stood out with 14 enforcement notices being given. One notice was issued in response to a control room operator who was found to have been dealing with over 100 ‘urgent’ alarms. Alarms are great, but they should always have a defined operator response. Without that, they have limited value.
Process safety competency is the final area I’d like to highlight. Of the enforcement notices issued, many involved at least one decision made onshore that was part of the incident or action. So, if you’re an employer or employee who thinks health and safety is someone else’s job, or the responsibility of the team offshore, then think again.
I’m not saying we all need to have the same level of process safety competence, but preventing major accidents really is a team effort. If you are making decisions that directly or indirectly influence the health and safety of others, then you need to understand the implications of those decisions.
I’ve experienced companies where process safety education is mandated for all employees but, on the flip side, I’ve also met people working on- and offshore who, whether through their own volition or the discretion of their employer, do not know about process safety to the extent you might expect. The IChemE’s Process Safety Competency Guidance is a good reference here, outlining the levels of competence required across many different roles – both operational and functional.
From my perspective, the three things we need to focus on are: process isolations and hydrocarbon releases, alarm management and competence. The engine warning light is on, and we can’t afford to ignore it.
While the COVID-19 pandemic has undeniably affected planned maintenance programmes and safety audits, by making sure the right people have the right information at the right time, and the demonstrable competence, we can continue to make inroads in improving our industry’s safety performance.
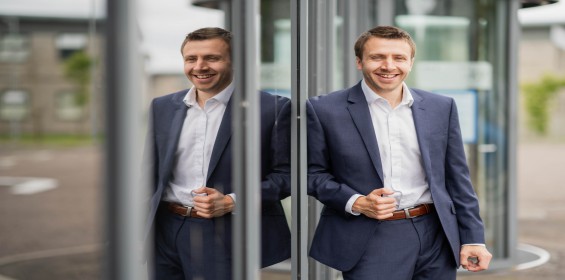