Investment in human skills key to optimising wind project returns
Published: 07 January, 2021
Rakesh Maharaj, CTO, ARMSA Academy
Since 2010, the UK wind sector’s capacity has more than quadrupled from 5.4GW to 24GW at the end of 2019, with offshore wind capacity in particular expanding by over 600%.
But the exponential growth has not come without its own challenges. Whilst government subsidies and ambitious targets have accelerated the development of the sector, wind farm owners have been forced to undertake significant cost-cutting to make the industry competitive with other energy sources.
Though the lower levelised cost of electricity has been good news for UK energy customers, wind owners, operators and contractors have become increasingly squeezed - with more electricity needing to be produced, and at lower costs.
Operational efficiency has become a key priority as a result, with the wind industry investing significantly in digitalisation in the form of machine learning, predictive maintenance and remote monitoring in order to optimise turbine performance.
In the same vein, the costliest aspects of wind operations have been reduced, particularly labour, resulting in a lack of talent development at all levels. According to the European Risk Observatory’s 2013 ‘Occupational safety and health in the wind energy sector’ report, the UK and EU wind sector could face a shortage of up to 28,000 appropriately qualified wind employees by 2030.
This is despite the fact that both on-site and off-site employees play a crucial role in the construction, maintenance and efficient operation of wind turbines.
Digital asset management and performance monitoring tools have come a long way in the past ten years, but they remain only as effective as the person using them.
On any given day at an offshore wind site, scores of decisions are taken by humans, not machines. Training personnel to interpret turbine data and the many fruits of digitalisation remains a key aspect of optimising asset performance. It makes no sense for asset owners to invest heavily in digitalisation without also investing to nurture a culture of informed human decision-making.
With Boris Johnson recently committing to increase the UK’s offshore wind capacity to 40GW by 2030, the industry must take a longer-term approach and recognise that investment in human performance, alongside digitalisation, represents a more effective route to optimising wind projects.
This is a sentiment shared by a number of European industry leaders such as Vattenfall, MHI Vestas and Siemens Gamesa. You can read more about their views here.
Investing in digital training approaches
Traditional training methods in the wind sector have focused primarily on developing skills in a classroom setting, typically at the beginning of an individual’s employment.
But even if over-stretched teams are still able to spare human resource to offsite training, the retention of ‘book knowledge’ for when it is needed in the course of day to day work months or even years after first learning it, can prove unreliable.
What’s more, personnel need to evolve and enhance their knowledge and aptitude for decision-making, as new technologies, problems and opportunities emerge. The wind industry is far from static!
Fortunately, change is coming.
Workflow learning - where employees’ learning fits around their working day - has become a buzzword in training publications but is yet to be applied in the wind sector, to any meaningful degree.
Today’s training platforms must be easily accessible, on-the-job and in-the-moment. They need to steer individuals daily, helping them to overcome challenges as they arise in the field. They need to promote real life examples of best practice and shared experience in order to maintain the highest standards of operation.
One example of this approach is ARMSA Academy, a bespoke digital performance support platform that has been adapted to a range of wind industry roles, from technicians to project managers, enabling them to learn vital skills during the daily flow of their work.
It’s an approach that uses technology to improve the daily decisions taken at all stages of the project life cycle. Triallists across the board have agreed that by promoting informed decision making in this way, available on and off-site at the touch of a button, asset owners and operators are also enhancing project safety, efficiency and productivity.
In short, digital performance support can help the wind industry to further reduce, safely, levelised costs in both construction and operation.
The UK offshore wind sector is set to scale exponentially, with government targeting the creation of some 60,000 jobs by 2030. It’s an opportune time for project owners and operators to re-examine how they equip their teams with the skills, knowledge and support they need in order to contribute fully to project performance.
Investing in digital performance support as well as digitalisation - we’re calling it a ‘Great Leap Forward’ for the productivity of offshore wind projects.
UK wind is entering another transformational decade, but the learning approaches which got us here will not be enough to get us where we need to be in 2030.
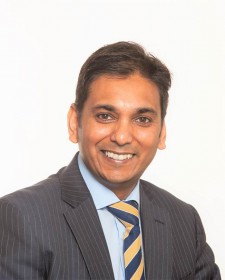