Pragma to begin P&A field trials for the oil and gas industry’s first additive manufactured, ultra-high expansion bridge plug
Published: 19 November, 2020
Aberdeen-based, oil and gas production technology business, Pragma, says it has combined innovative design and additive manufacturing (AM) techniques to bring the industry’s first 3D metal printed, ultra-high expansion, bridge plug to market. Pragma’s patented M-Bubble bridge plug has successfully completed final lab testing and is due to begin field trials by the end of 2020.
Initially targeted at both the P&A sector and water shut off applications, the first M-Bubble bridge plug addresses a gap in the market for a lower cost, fast-turnaround, permanent plugging solution, with a high (3,000psi) pressure differential capability. The plug can be set without additional cement to save rig time and ‘waiting-on-cement’ time, which can accumulate significant savings for the operator especially in deeper, extended reach wells. This capability also provides barrier integrity reassurance when there is the possibility of a poor cement bond or cement channelling occurring on the high side of deviated wells.
The company says the exceptional strength imparted by additive manufacturing, using specialist Inconel alloy, plus the ultra-high 300% expansion ratio of the M-Bubble bridge plug, provides a robust and reliable plugging solution for large internal casing diameters. For example, a 2.625” outer diameter plug can be run through a 3.5” tubing string, navigate internal restrictions and then be expanded into a compliant shape within a 7” casing.
Appealing to a broad global market of both operators and service companies, Pragma has designed the bridge plug to be universally suited to industry standard mechanical or pyrotechnic setting tools, run on slickline, electric line or coiled tubing.
Following an intensive R&D programme, Pragma says it has designed and manufactured the M-Bubble bridge plug in line with established AM codes and guidelines, as well as emerging oil and gas specific AM codes such as DNVGL-ST-B203. Prototype production has demonstrated extremely high levels of repeatability, not found in conventional machining, and the AM process can halve delivery times so products are produced on demand, resulting in less stockpiling and lower costs.
Stuart Cowen, technical sales manager, at Pragma added: “We are now in discussion with a range of parties who are interested in collaborating to develop the M-Bubble range further. The next stage is the addition of slips, to achieve ISO 14310:2008 V3 rating. The V3 trials will also test the internal mechanism that makes the plug retrievable, which is currently disabled for cost-effective P&A deployments. Introducing retrievable plugs will extend the product capability to zonal isolation applications and temporary water shut-off in horizontal wells. Retrofit high expansion solutions for slimmer 3.5” completions are also required by operators to extend the life of wells and fields where surface production facilities might be unable to cope with increasing water production longer term. These are all areas where we see significant operator benefits and we’re looking forward to continuing our commercialisation programme with a range of partners.”
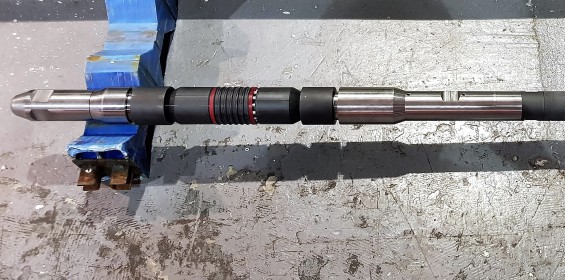