Re-evaluating tech legacy use in the oil and gas industry to support rapid market recovery
Published: 30 October, 2020
With 2020 set to be a transformative year for the offshore oil and gas industry, asset owners must walk a tightrope between short term cost cutting, and long-term investment that fuels rapid downturn recovery. Graeme Turnbull, system product manager at AAF International, reports.
For the oil and gas industry, 2020 has been a year of stark contrasts so far. After a promising start buoyed by the sector’s recovery from the 2016 price crash, the onset of COVID-19 and the subsequent Russia-Saudi Arabia price war has triggered unparalleled uncertainty and economic turmoil. While oil price volatility has eased slightly due to rising demand, the road to recovery and the “next normal” is already triggering consolidation, deep budgetary cuts, as well as growing societal pressure to decarbonise, in line with wider calls for a “green-led” economic recovery from COVID-19.
According to the Energy Industries Council (EIC), operators are responding to the crisis by seeking spending cuts of 20%-30%, with reductions likely to span the rest of this year and next. As an inevitable result of this, the supply chain will be asked to trim the cost of its services – a move that will pose fresh challenges for businesses that were already required to deliver substantial efficiency gains during previous price crashes. The urgent need to save cash comes with a cautionary tale from the EIC. In its recent report “Survive and Thrive”, the trade association advises against blunt cost-cutting which can impact core capabilities and functions, resulting in a slower business recovery. Instead, it advocates a downturn response that involves protecting key assets by continuing to invest in business development, employees and technology. When it comes to managing the expectations of operators asking for discounts from suppliers, the EIC further advocates a so-called “solutions space”, where operators and suppliers work in partnership. This involves engaging at a senior level to gain a deep understanding into the current situation and mutually agreeing what’s possible – in terms of competitive pricing, and overarching approach. Put simply, the days of brochures and price lists could now be over, as the sector adapts to what many believe is a “lower forever” oil price, rather than a “lower for longer” scenario, like we have seen following previous oil price crashes.
Complex decisions. Decisive action
While offshore operators may be united in their desire to squeeze budgets, it should be acknowledged that developing and executing a prudent cost cutting strategy that maintains (and even enhances) critical business functions is not easy. With a full appreciation that the solution(s) will likely be multi-layered, we would argue that one area operators should focus on is overhauling legacy technologies. This includes examining their role on offshore platforms, plus an assessment of whether new, proven solutions can discharge the same responsibilities in a more efficient and effective way. One example of this is air filtration technologies, which have the ability to exponentially enhance gas turbine performance and availability while promoting better compressor cleanliness and long-term part integrity.
Traditional approaches
Currently, around 85% of offshore gas turbines are protected by small high velocity filtration systems that utilise low efficiency filter bags, which only provide adequate protection against large coarse particles, and fail to capture the majority of sub-micron particles offshore. It is worth noting that this scenario traces its roots back to the 1970s when the National Gas Turbine Establishment (NGTE) located at Pyestock, England, published technical paper 59/1975 for ocean going vessels, later to become known in the offshore industry as the ‘30 knot aerosol’. The research was taken less than 10m above sea level on a Royal Navy frigate. The measuring equipment was also appropriate for the time and concluded 95% of particles are >5 microns, with the majority bigger than 13 microns. In the world of filtration these are very large particles and why smaller filtration systems with low efficiency bags were highly appropriate. However, fast forward to 2017 and recent measurements at platform height (which is often >30m) with modern measuring equipment tell a different story. It is in complete contrast to the NGTE research with 75% of particles in the North Sea smaller than 0.3 microns and in the Middle East that percentage increases to 97%. This is why low efficiency filter bags are not suitable for this environment, in the onshore environment these bags are now only used as pre-filters to protect intermediate and final filters.
The legacy of this situation has resulted in lost production revenue, unplanned gas turbine shutdowns and costly downtime, reduced component and engine life, premature engine failure, and low turbine compression efficiency as well as high CO2 emissions. All of these impacts are significantly magnified and unwanted given today’s current market dynamics and the low price of oil. What’s more, small high velocity systems are designed to allow water, moisture or fog to coalesce as it passes through the filter bags. This process creates larger droplets which are designed to be captured by a downstream vane after the filter bags. However, vanes are not 100% efficient and some of the water and salt in solution will pass through the vanes. In addition, water will often collect on the floor downstream of the bags and upstream of the final vanes. The salt laden water will evaporate over time, which will allow salt crystals to enter the airstream and hence a proportion of these dry salt crystals will pass through the vanes into the gas turbine.
By contrast, high Efficiency Particulate Air Filter (EPA) E12 technology captures 99.95% of 0.3 micron particles, compared with low efficiency filter bags which only capture 5% of particles at this size. This significantly protects and enhances the performance of expensive gas turbine components. As offshore operators have become aware of the benefits of EPA E12 air intake filtration, there has been a push to upgrade existing high velocity units installed offshore. However, traditional EPA E12 filtration technologies - with much larger equipment envelopes - have necessitated that the air intake filter system is replaced in its entirety. This increases foundation loads and incurs significant costs and downtime. However, there is another route, using a new revolutionary EPA E12 system which provides all the associated benefits of EPA E12 air filtration, but can be quickly and seamlessly installed within the existing high velocity air intake filtration system.
BP Clair
The BP Clair platform operates three Titan 130 gas turbines (GTs 1, 2 & 3) employed in power generation application to provide power to the asset. Each gas turbine was experiencing compressor blade fouling, corrosion and erosion, as well as turbine section hot gas path corrosion. Operationally, this resulted in poor engine reliability, reduced availability and premature engine overhaul and/or replacement. All of which severely impeded the long-term strategic planning for the platform for both production and maintenance.
Eventually, the poor filtration provided by the high velocity bag system resulted in a catastrophic failure of GT2 after 12,000 operating hours, which equated to only a 1/3 of the engine design life. The root cause of the failure being inlet guide vane seizure and in turn compressor section imbalance and ultimately blade liberation. This resulted in irreparable damage and a new replacement engine was required, incurring unplanned long-term shutdown and significant unbudgeted costs.
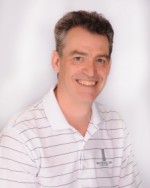
BP was aware that AAF International was in the final stages of developing a new EPA E12 high velocity filtration solution. Critically this new design could be installed within an existing high velocity housing, therefore negating the need for a larger housing replacement. As a consequence of this failure on GT2, BP was expediting the GT OEM (Original Equipment Manufacturer) for fast-track delivery of a replacement engine and approached AAF to determine if this new technology (N-hance® Performance Filtration) could be urgently deployed in a field trial as a technology collaboration initiative.
Thanks to a longstanding previous relationship between the two companies, BP was able and confident to pilot AAF’s N-hance technology. The N-hance filters and conversion parts were delivered to BP within 5 weeks and commissioned along with the new GT2 engine on BP Clair in February 2017.
The pilot delivered excellent results. There was a significant increase in engine availability resulting from a reduction in unplanned downtime and shortened shutdown periods. There was also a decrease in CO2 emissions improving sustainability, as well as retained power output (compressor efficiency) and heat rate. Critically, BP has also eliminated the risk of potential GT failure due to corrosion.
Commenting on the project, BP’s asset team said: “The upgrade project has enabled improved reliability, cost savings and will feed into the reformation of outdated air filtration standards as well as playing a part in helping to achieve offshore asset efficiency of 90%.”
Transition from asset-by-asset to a widespread role out
BP’s Clair platform in the North Sea, demonstrates the optimum role air filtration systems can play in unlocking considerable financial, operational and environmental benefits. While the pilot results from BP Clare are both tangible and compelling, air filtration, like other technologies, could deliver wholesale benefits faster if rolled out on a widespread, rather than an asset by asset basis. There is still considerable work to do before this vision can be realised. Assets owners need confidence that new solutions provide acceptable and ideally low levels of risk and must have a full understanding of the lifecycle benefits in offer. The ability of chosen technologies to operate safety offshore, and in a way that supports wider energy security and decarbonisation efforts, should also be well understood.
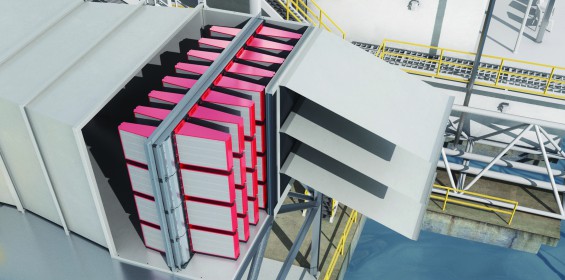