Adhesives assure hydraulic systems' reliability
Published: 11 June, 2020
A gigantic Berg Propulsion propeller with a diameter of more than nine metres dwarfs the men standing next to it and at every stage of its manufacture, LOCTITE engineering adhesives from Henkel have an important part to play.
LOCTITE threadlockers and thread sealants secure assemblies in the hydraulic systems in the propeller hub. The systems have to be pressure resistant and threaded assemblies immune from vibration loads. Indeed, a minimum of 25 years of reliable service is the expected norm.
“Our customers require ship propulsion systems with the highest availability at all times,” explained Anders Christofferson, managing director of Berg Propulsion Technology AB. “LOCTITE increases the reliability of our products. The products allow quick and easy assembly and we also rely heavily on Henkel’s technical support.”
The thread of the hydraulic pipes responsible for controlling the individual blades are retained by LOCTITE 638. They have to withstand more than 70 bar of oil pressure which equals twice the force the blades will have to bear at sea. The adhesive sealing has to create an hermetic seal after an hour because the hydraulic pipes are then embedded into the shaft.
LOCTITE 638 is a high strength retaining compound that is said to provide the best resistance to dynamic, axial and radial loads. Applied as a liquid it forms 100% contact between mating metal surfaces and provides many advantages over conventional assembly methods. It floods into the inner spaces between components, curing to form a strong, precision assembly.
A typical use for LOCTITE threadlocking is on a spacer that protects the propeller’s control units. The spacer is fitted in place with four screws and locked with LOCTITE 243. Other applications for this product include securing end cap fixings and dowel pins to prevent self-loosening and in general pipe assembly
LOCTITE 243 is a medium strength threadlocking adhesive that is suitable for joining all materials including passive substrates such as stainless steel, aluminium and plated surfaces. As a single component it is clean and easy to apply that cures at room temperature to a hard, solid thermoset plastic.
“We started using LOCTITE in 1964,” Anders Christofferson continued. “Erik Berg, son of the company’s founder, brought a LOCTITE product back from the UK as a replacement for the locking washer and it worked.” LOCTITE has underpinned the reliability of Berg Propulsion products ever since.
Henkel’s continuous development of core products such as threadlocking adhesives have seen the introduction of many upgrades and new developments since 1964. For example, today’s choice includes Health and Safety formulations that carry hazard-free labelling.
The technical performance of the products also been also extended. Threadlockers can now tolerate higher operating temperatures and are tolerant to oil, making them less sensitive to improperly cleaned parts. And importantly, these qualities have been achieved without compromising any of the products’ other key properties such as chemical resistance and shelf life.
Threadlockers are also now available as semi-solid adhesives, in stick form, as well as a wide range of different liquid viscosities and strengths to suit the application. Another important development is the introduction of new packaging to minimise the risk of users unwittingly using inferior, counterfeit products that could compromise application success.
For more information go to: www.henkel-adhesives.co.uk
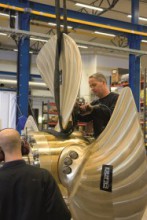